Choosing the right connecting rods for your engine is a pivotal decision that can significantly impact its performance, durability, and overall efficiency. In the world of high-performance engines, where every component plays a crucial role, understanding the intricate factors involved in selecting connecting rods is paramount. This comprehensive guide explores the critical aspects that shape the choice of connecting rods, providing you with the insights needed to make an informed decision tailored to your engine’s unique requirements.
Factor 1: Engine Performance and Output Power
The first and foremost consideration in selecting connecting rods is your engine’s performance demands. This encompasses factors such as horsepower, torque, and the desired range of rotational speeds (RPM). Connecting rods are subjected to immense forces generated by the engine’s power output, and selecting rods capable of withstanding these stresses is crucial. Understanding your engine’s power needs is the initial step towards matching the right connecting rods to your engine’s performance aspirations.
Factor 2: Engine Size and Configuration
Engine size is a pivotal factor that directly influences the choice of connecting rods. This includes vital measurements like piston height and crankshaft stroke. A harmonious synergy between connecting rod dimensions, piston characteristics, and crankshaft specifications is essential for optimal engine performance. Proper alignment ensures that the connecting rods function seamlessly within the engine block, contributing to improved combustion efficiency and overall power delivery.
Factor 3: Application and Racing Environment
The intended application of your engine plays a pivotal role in determining the ideal connecting rod configuration. Whether your engine is destined for street racing, endurance racing, or daily commuting, each application demands specific attributes from the connecting rods. Factors such as stress levels, durability requirements, and the intensity of the racing environment all influence the choice of connecting rods that will thrive under these conditions.
How can I prevent damage to the piston rod in my Jetski and ensure it is functioning optimally?
Factor 4: Piston Weight and Balance
The weight of the piston is intrinsically linked to the choice of connecting rods. Achieving a harmonious balance between piston weight and connecting rod specifications is essential for the engine’s overall stability and longevity. A well-matched combination minimizes wear and stress on various engine components, ensuring smoother operation and extended service life.
Factor 5: Budget Considerations
Practicality and budget are pivotal aspects that must be factored into your decision-making process. Connecting rods come in a range of materials, configurations, and price points. While high-performance materials can offer superior strength, they might come with a higher cost. Evaluating your budget constraints alongside your performance goals is essential for arriving at a well-rounded decision that aligns with both your engine’s needs and your financial considerations.
In conclusion, selecting the right connecting rods for your engine is a multifaceted process that demands a deep understanding of your engine’s performance requirements, size specifications, intended application, piston weight, and budget limitations. By meticulously evaluating these factors, you can make an informed choice that optimizes your engine’s power output, durability, and overall performance. Connecting rods serve as a crucial link between your engine’s aspirations and its mechanical execution – a decision not to be taken lightly.
Why choose Kingtecjetski connecting rod and piston?
Let’s explore the intricate nuances of connecting rod designs even further.
Conventional I-beam connecting rods, commonly found in stock engines, can capably accommodate power outputs of up to approximately 400 horsepower and rotational speeds of around 6,500 RPM. However, as you venture into the realm of high-performance engines, surpassing these thresholds becomes the norm. This is where aftermarket connecting rods step in, offering a range of materials and designs to meet these escalated demands.
Aftermarket I-beam rods come into their own, particularly when constructed from advanced materials such as forged steel, titanium, or aluminum alloys. These materials possess exceptional compressive strength, making them the prime choice for high-powered engines. Notably, I-beam designs often have the advantage of being lighter than their H-beam counterparts, contributing to reduced reciprocating mass and enhanced engine response.
The H-beam connecting rod design stands as a testament to engineering innovation. It employs a distinctive approach to enhance both stiffness and overall strength. With its twin flat sides and a slender cross-section connecting them, H-beam rods create a solid structure that excels in managing compressive forces. However, this enhanced strength often comes at a cost, as H-beam rods are generally more expensive to manufacture and acquire.
In the grand scheme of things, the choice between I-beam and H-beam connecting rods hinges on a multitude of factors. It’s essential to weigh the performance requirements, budget constraints, and even the specific racing environment. If you’re looking for the pinnacle of structural integrity and can accommodate the associated cost, H-beam rods emerge as the frontrunner. However, for those seeking a balance between performance and affordability, advanced I-beam rods offer a compelling alternative.
Ultimately, connecting rods serve as a vital bridge between your engine’s power production and its mechanical stability. Understanding the intricate differences between I-beam and H-beam designs empowers you to make an informed decision that aligns with your engine’s unique demands and your overall racing aspirations.
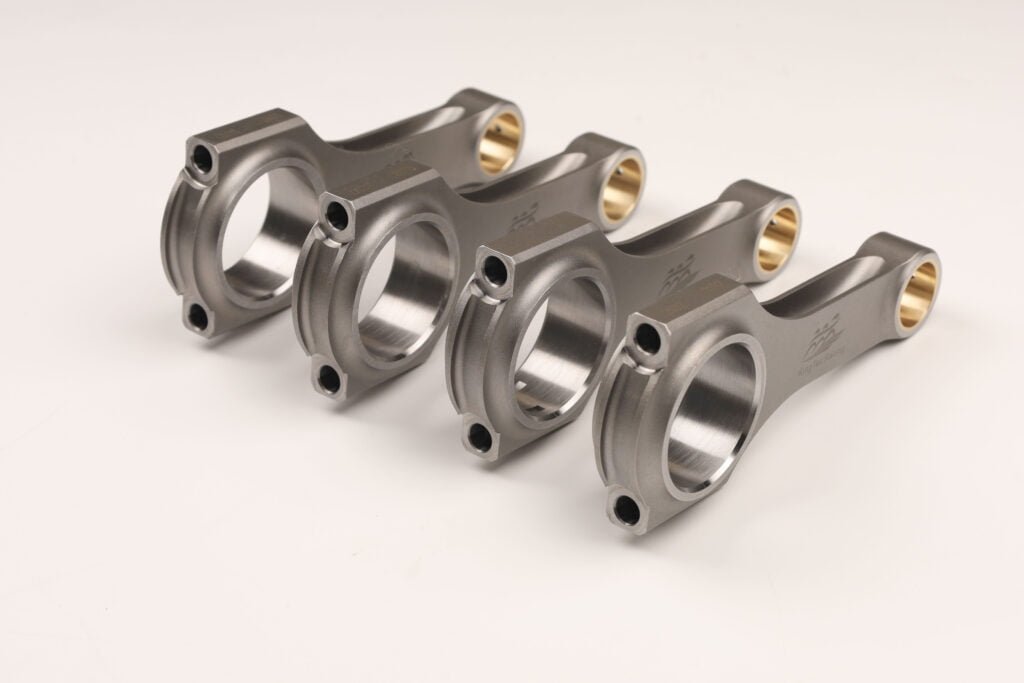
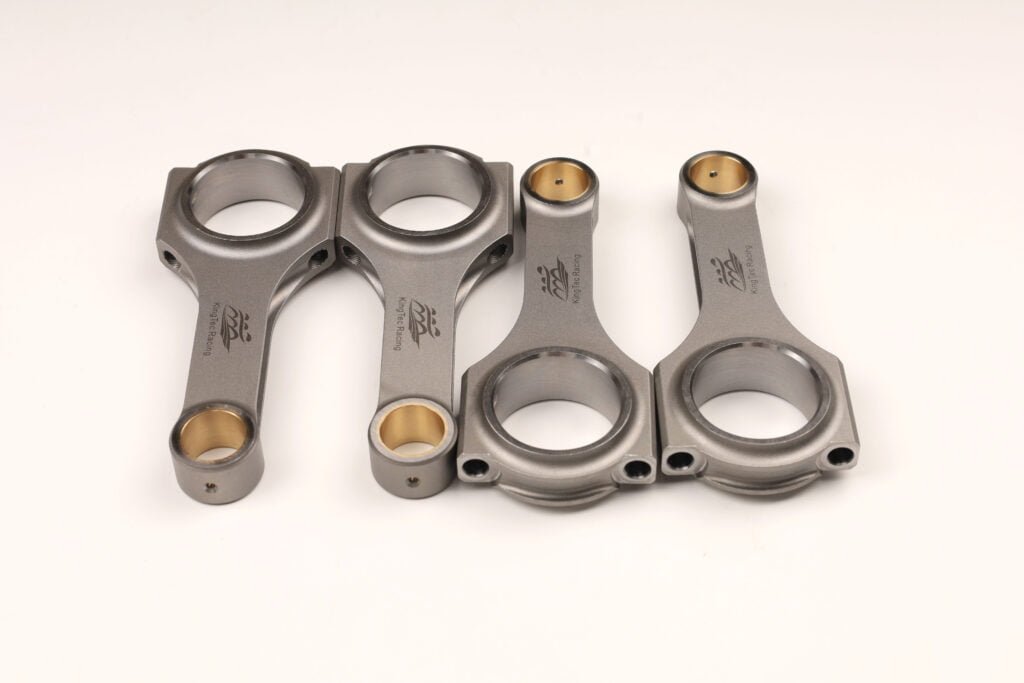
Three main materials for connecting rods
When it comes to selecting the right material for connecting rods, a range of options is at your disposal, each with its unique set of advantages and drawbacks.
Steel, aluminum, and titanium are the three primary contenders in the world of connecting rod materials. Steel connecting rods are a common choice, with most aftermarket options being forged from this durable material. However, not all forged steels are created equal; their composition can vary significantly based on the grade of material. To illustrate, Eagle Specialties employs 5140 steel for their entry-level rods, while for more intense competition demands, they, along with many other manufacturers, turn to the high-carbon strength of 4340 or 4330 steel.
Aluminum connecting rods offer a distinct advantage: they can weigh up to 25 percent less than their steel counterparts. This weight reduction holds immense appeal for racers aiming to minimize reciprocating mass. As a result, engines equipped with aluminum rods can rev higher and faster, translating into increased power output. However, the trade-off here lies in the fatigue life of aluminum rods, which is generally shorter compared to steel.
Enter titanium, the third alternative. Titanium connecting rods strike a balance between the lightweight attributes of aluminum and the robust strength of steel. This unique combination makes them particularly enticing for vehicles like drag cars or sprint cars that demand rapid throttle response and supreme power-to-weight ratios. However, it’s worth noting that the allure of titanium comes with a hefty price tag, positioning it as a premium option in the connecting rod market.
In the end, the choice of connecting rod material hinges on a delicate balance between performance, durability, and budget considerations. Each material has its own merits, and understanding the nuances of steel, aluminum, and titanium can empower you to make an informed decision that aligns perfectly with your racing aspirations.
So which connecting rods would you choose?